Safety Workshops
Safety Workshops Services
Hazard and Operability (HAZOP)
What is HAZOP?
A step by step qualitative analysis of various process sections (or nodes) to identify the potential hazards and operability issues associated with it.
The approach is a workshop based activity comprising of a multi-disciplinary team with external Facilitator to lead the discussion with the HAZOP guidewords. The team will systematically review the process drawing details and determine the significant issues which are likely to occur in the event of process deviations from the design intention as well as the consequences.
The adequacy of the safeguards will be assessed and if it is deemed insufficient by the team, additional safeguards will be proposed for implementation into the design. The salient points, safeguards, and recommendations during the workshop session will be recorded in HAZOP Worksheet which will be attached in the HAZOP Report.
Why do HAZOP?
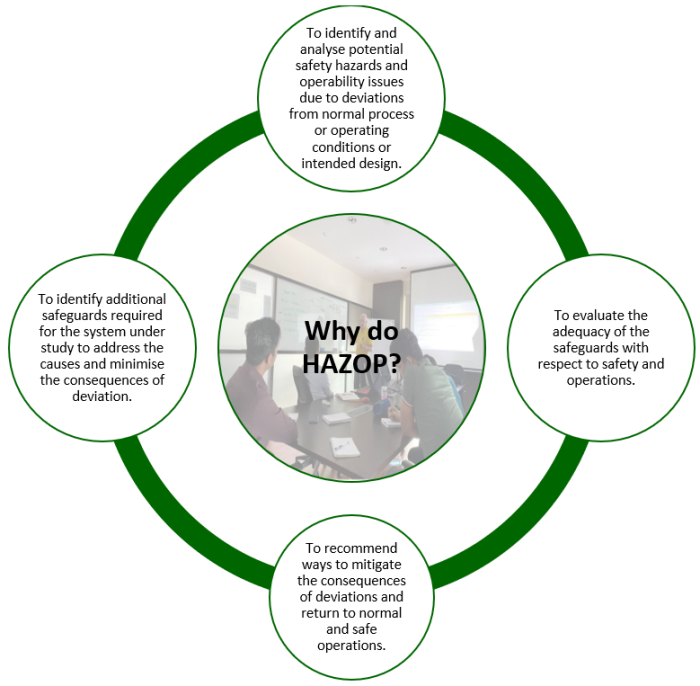
Methodology
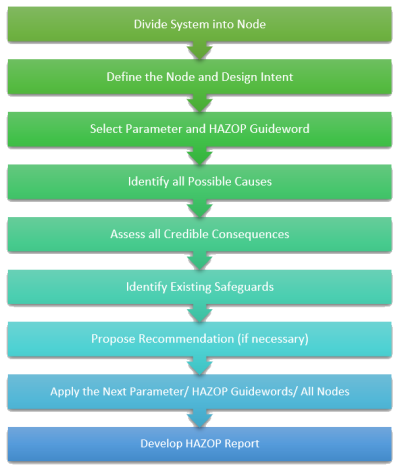
HAZOP Preparation
The following documents are required for workshop preparation:
- PFD and P&IDs
- Heat and Material Balance
- Design Basis Memorandum
- Cause and Effect Diagrams
- Process Design Basis
- Process Operation and Control Philosophy
- Equipment Layout/ Plot Plan
- HAZOP Worksheet
HAZOP Attendance
- Facilitator
- Scriber
- Process Engineer
- Mechanical Engineer
- Operations Personnel
- Project Engineer
- Piping Engineer
- Structural Engineer
- Electrical/ Instrument Engineer
- Technical Safety Engineer
- Maintenance Engineer
- Instrument Engineer
Standards & Regulations
- COMPANY’S HAZOP Standards/ Guidelines.
Hazard Identification (HAZID)
What is HAZID?
HAZard IDentification (HAZID) is a well-known risk assessment and management tool that can be used to identify inherent hazards and risks in a complex process or system. A HAZID evaluation is used to identify potential dangers and drawbacks in the plant, system, operation, style, and maintenance.
The method is a design-enabling tool, acting to help organize the HSE deliverables in a project. The structured brainstorming technique typically involves designer and client personnel engineering disciplines, project management, commissioning and operations. The main major findings and hazard ratings help to deliver HSE compliance, and form part of the project Risk Register required by many licensing authorities.
Why Do HAZID Study?
A well-organized HAZID study activity will deliver a good identification of hazards and safeguards at an early stage in the design of a facility. Team output helps ensure that:
- HSE hazards are revealed at an early stage in the project, before significant costs have been incurred
- Hazards are recorded and actioned so that they can be avoided, mitigated or highlighted
- Establish safeguards to manage hazards; identify areas where further understanding of safeguard effectiveness is needed
- Any specific process modifications if required can be established at an early stage
- Any special preparations required to be taken to handle these can be pre – planned
Safety Integrity Level (SIL/IPF) Classification and Verification
Safety Integrity Level (SIL) Classification
What is? And why we do?
Safety Integrity Level (SIL) Classification is a practice of allocating or assigning a desired/target SIL level to a Safety Instrumented Systems (SIS) or Safety Instrumented Function (SIF) installed in Process Plants. A SIL is a measure of safety system performance, in terms of probability of failure on demand (PFD) or risk reduction factor (RRF). The desired/target SIL level that is determined during SIL Classification conveys (1) the permitted likelihood of an instrument or safety function fails to perform its design function when required/during hazardous event or (2) the level of risk reduction that a SIF must provide to achieve an acceptable risk.
There are four different integrity levels associated with SIL. The higher the SIL, the higher the associated safety level, and the less likely a system will fail to function properly. As the SIL level rises, so do the system’s installation and maintenance expenses, as well as its complexity.
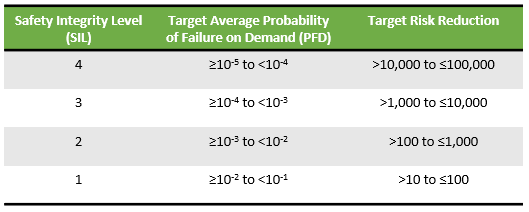
Approach
A SIL Classification is performed in a workshop to enables a team of qualified and experienced engineers to determine a SIL level, based on relevant criteria and analyses for each control or safety loop. In the process industry sector, LOPA method are frequently selected for determining SIL requirements instead of Risk Graph method. The LOPA method provides specific criteria for evaluating Independent Protection Layers (IPLs), which eliminates subjectivity of the qualitative approach.
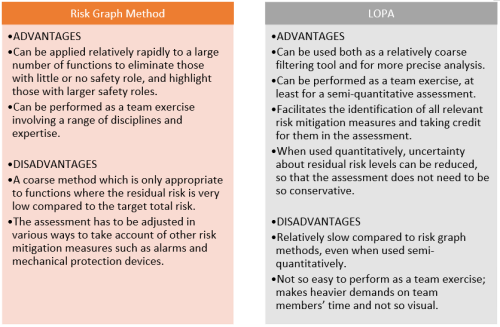
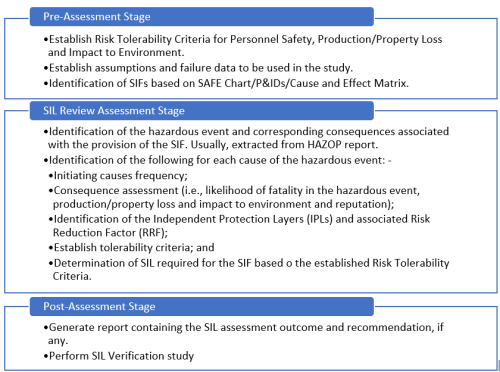
Standards / References
- IEC 61508: Functional Safety of Electrical/Electronic/Programmable Electronic Safety-Related Systems
- IEC 61511: Safety Instrumented Systems for the Process Industry Sector
Software
- Excel spreadsheet
- exSILentia by EXIDA
Safety Integrity Level (SIL) Verification
What is? Why we do?
The process of verifying whether the design of the automated safety system or Safety Instrumented Function (SIF) is adequate to achieve the required failure performance or integrity level as determined during SIL Classification. SIL Verification usually conducted on a SIF classified as SIL 1 and above.
The main assessment for this verification exercise is the Probability of Failure on Demand (PFD) and Architectural Constraint associated with the SIF. Once a SIF meets the requirement in both assessments, then the SIF is deemed to meet the target SIL. Each SIF consist of three main elements, i.e., sensors, logic solver and final elements. Even though one of the elements is certified as SIL 2 or 3 by the supplier or vendor, doesn’t mean that the whole loop or SIF is automatically verified the same.
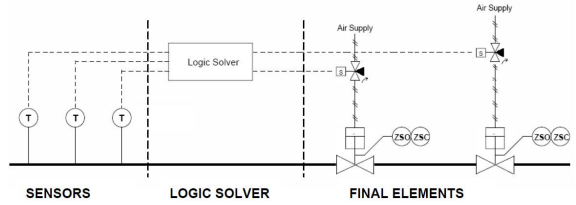
Approach
A typical methodology for SIL Verification is shown below.
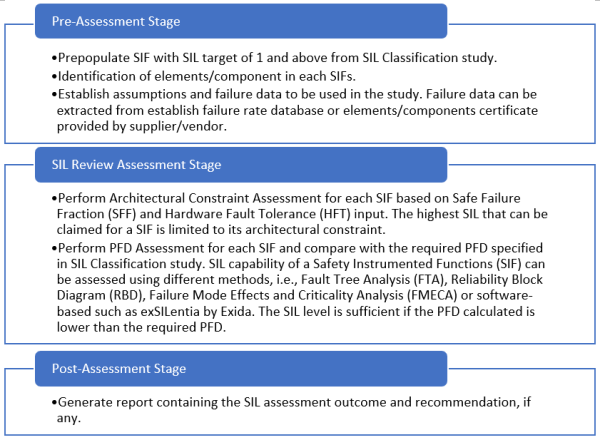
Standards/References
- IEC 61508: Functional Safety of Electrical/Electronic/Programmable Electronic Safety-Related Systems
- IEC 61511: Safety Instrumented Systems for the Process Industry Sector
Software
- Excel spreadsheet
- exSILentia by EXIDA
Electrical Safety and Operability (ELSOR/SAFOP/EHAZOP)
What is ELSOR?
The application of a series of technical examinations and audits of high voltage generation, transmission, and distribution of electrical systems to assess the hazard potential to personnel and plan of mistaken system operation or malfunction of individual components and consequential effects, including operator error. It may also be referring to as Electrical System Safety and Operability (SAFOP) of Electrical Hazard Operability (E-HAZOP).
For PETRONAS facility and partners, P-ELSOR is applied which will include 2 items of study:
- Electrical Safety, System Integrity & Robustness (ESSIR) which assess the integrity, robustness and operability of electrical system and equipment; and
- Electrical Safety, Task & Operational (ESATO) which assess the potential electrical hazards due to human activities and errors.
Why do ELSOR?
The purpose of ELSOR or E-HAZOP is to identify all electrical network hazards and operability issues. This assessment may focus on the more hazardous side (i.e. high-voltage distribution system), which includes the primary electrical generating (or distribution source) as well as other electrical interfaces documents (include but not limited to – Single Line Diagrams, Equipment Schematics, Lighting System, Electrical Room Layout, Substation Layout, Cable Layout, Earthing Layout, Hazardous Area Classification and etc).
Health Risk Assessment (HRA)
What is HRA?
Health Risk Assessment is the most used method for detecting and classifying occupational health risks, as well as the level of risk they pose to humans in the workplace. Hazards can be controlled or avoided by offering recommendations based on the findings of the investigation to provide a safe working environment. The HRA study will examine possible control strategies in order to assess the risks and make recommendations for future hazard reduction.
Why do HRA?
The process of identifying the dangers and impacts connected with a particular activity or facility, as well as analysing the risk posed, with the goal of eliminating or lowering the risk to the lowest level reasonably practicable (ALARP). The health identification inventory, risk prioritisation summary, and control measures are all part of the HRA study. The risk assessment study must provide a list of specific work processes and other measures to handle HSE hazards. Potential emergency scenarios will be identified, and strategies for dealing with them will be included in the research.
Constructability Review (CR)
What is CR?
The Constructability Review (CR) is the application of a formal, systematic, and structured review procedure for the critical examination of the risks associated with construction, installation, and hook-up activities under evaluation.
CR will be carried out in a workshop forum, employing an experienced multidisciplinary team led by an approved Facilitator. The CR process is a structured brainstorming exercise. The Facilitator is responsible to coordinate and guide the discussion to identify any arising issues.
Why do CR?
The objective of the Construction Review is to evaluate constructability during the pre-construction or at early design phase (i.e. Concept selection etc.). This constructability evaluation helps to identify any issues before the actual construction begins and helps to minimize errors, delays and overhead. Construction Review Also will identify improvements/modifications to meet the requirement of the project mainly on the safety and constructability/ installation aspects