Loss Prevention Studies
Loss Prevention Studies Services
Firewater Demand and Hydraulic Analysis
Firewater systems are essential to the safety of many areas within the oil, gas and petrochemicals industry. Firewater Demand Study and Hydraulic Analysis are essential to ensure firewater is adequate during emergency. This study applicable for Offshore (Facilities and Vessels) and Onshore (Facilities and Buildings).
What is Firewater Demand Study?
Firewater Demand is an estimate of fire water required in the worst-case fire scenario in multiple locations concurrently in a facility. The demand uses input from Firewater System design such as P&IDs and Facility’s layouts. The determination of a facility firewater demand includes the minimum volume of water, design flow rate, maximum water velocity within piping and minimum pressure requirement as per COMPANY/Authorities guidelines/ regulations or Codes and Standards.
What is Firewater Hydraulic Analysis?
Hydraulic Analysis is performed to ensure adequacy of pressure, velocity and flow rate of a Firewater System as stipulated in Firewater Demand Study. This analysis can be carried out for an existing / prospective facility or any extension of an existing plant by utilizing designed piping network, instrument of the facility and water demand required for worst-case fire scenario by using a Software (Pipenet).
Surge Analysis (i.e., water hammer due the transient operations of the pumps and valves resulting in piping fatigue and failure) can be performed as part of the facility firewater hydraulic analysist to avoid any unanticipated failure when on demand.
Approach
Firewater Demand Study

Firewater Hydraulic Analysis
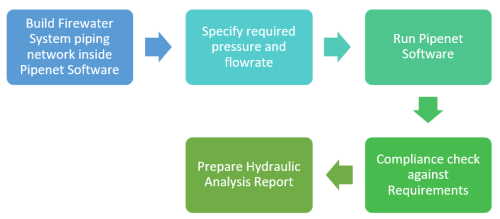
Software
- Pipenet
Codes and Standards
- Malaysian Standards (MS 1183, MS 1489, MS 2616 and etc..)
- National Fire Protection Association (NFPA 1, 13, 15 and etc..)
- PETRONAS Technical Standards (PTS 16.54.01, 16.73.01, 12.34.02 and etc.)

Hazardous Area Classification (HAC)
What is HAC?
The Hazardous Area Classification (HAC) is used to examine and classify the various sections of a facility depending on the presence of flammable materials. The HAC analysis identifies the facility’s hazardous and non-hazardous regions. It specifies where risks such as fire and explosion are likely to occur in the facility. The investigation is carried out using two systems. One is Class or Division system and other is Zone system.
The following are the three zones that hazardous regions are categorised into:
- Zone 0: A flammable atmosphere exists continuously or for extended periods of time.
- Zone 1: A flammable atmosphere is likely to occur during normal operations.
- Zone 2: A flammable atmosphere is unlikely to arise during normal operations, and if it does, it will only last a short time.
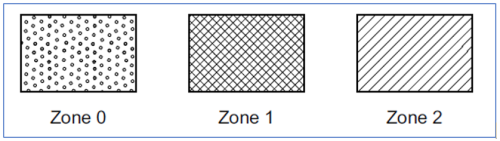
Why do HAC?
The primary goal of the Hazardous Area Classification study is to eliminate the existence of ignition sources in hazardous places, such as electrical devices. Combustible dust will cause fire and explosion if electrical equipment is present in an area where there is a probability of continuous or intermittent presence of Flammable substance liquid/vapour. Those areas are easily identified and categorized by this study.
Approach (Based on Energy Institute Part 15)
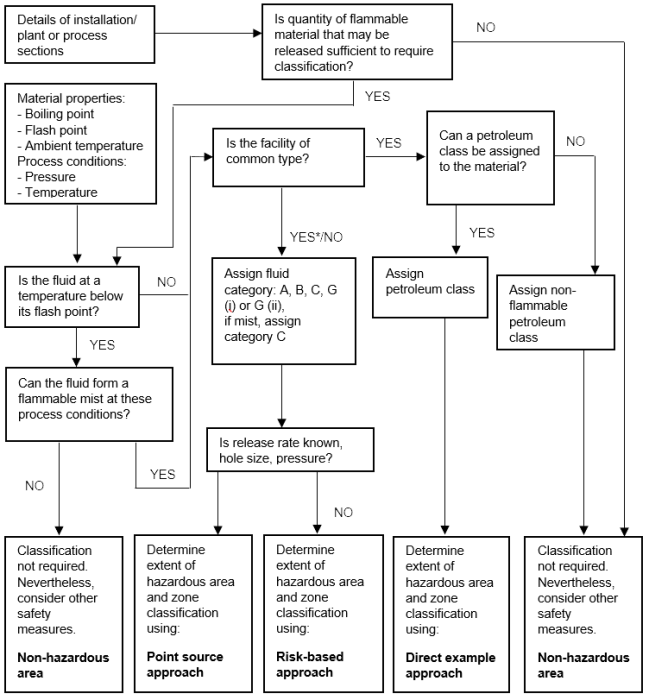
Codes and Standards
- Energy Institute Part 15 – Area Classifications
Safety Layouts And Drawings
For the facility’s safe and effective operation, the layout of working units, equipment, buildings, decks/floors, and roads is vital. The most efficient way to avoid an incident from escalating is to have a decent layout. It also gives emergency response services easy access.
Safety layouts and drawings are prepared to prevent or minimize the potential of death, personnel injury, and/or property damage that may result from any accident and emergencies. It is very important to have a clear and proper safety layout at each floor / level / deck at any facility to indicate the emergency evacuation path as well as the location of available safety equipment (i.e. firefighting equipment, eyewash & safety shower, first aid, etc.).
Safety layouts are required in all facilities (onshore and offshore) as to comply with the company’s and authorities’ codes & standards.
A compliant safety layout shall contain:
- Plan layout of the facility
- Assembly point(s)
- Escape routes
- Emergency exits
- Location of firefighting & safety equipment
- First aid equipment
- Fire panel
- Fire stairs
- Northerly point
At IPS, we have the capability to establish a comprehensive and technical safety layout by using the AutoCAD software. The example of typical safety layouts and drawings are as follows:
Safety Equipment Datasheet And Specification
Safety Equipment Datasheet and Specification is established to define the functional and technical requirement for the design, development, manufacturing, testing, supply, installation, inspection, performance, and storage of Fire Fighting Equipment, Life Saving Equipment, Safety/Escape Equipment, and Safety Signs of any facility and building.
All safety equipment must be provided with high degree of reliability and able to withstand various kind of operating and weather conditions. Sufficient data for all safety equipment are required for evaluation against the total life of field costs (i.e. capital equipment, spares, utility requirement, maintenance and loss of production) estimated to be incurred.
Listed below the examples of Codes, Standards, and Regulations that are to be in accordance with during the preparation of Safety Equipment Datasheets and Specification:
- ANSI / ISEA Z358.1 – Emergency Eyewash and Shower Equipment
- BS 2092 – Specification for Industrial Eye-Protectors
- BS 7944 – Heavy Duty Fire Blankets
- BS EN 1866 – Mobile Fire Extinguishers
- BS EN3:1996 – Portable Fire Extinguisher
- ISO 7010 – Graphical Symbols – Safety Colours and Safety Signs – Registered Safety Signs
- ISO 9001 – Quality Assurance
- LSA CODE – International Life Saving Appliances Code
- Malaysian Factories and Machinery Act, 1967
- Malaysian Environmental Quality Act 1974 (Act 127) & Subsidiary Legislation
- Malaysian Occupational Safety and Health Act, 1994
- MS 1539 – Specification for Portable Fire Extinguisher
- NFA 70E – Standard for Electrical Safety in the Workplace
- NFPA 10 – Standard for Portable Fire Extinguishers
Figures below are examples of Safety Equipment Datasheet:
Fire Safety Assessment, Fire and Explosion Strategy (FES) & Fire Safety Adequacy Review (FSAR) (Onshore)
What is Fire Safety Assessment?
A Fire Safety Assessment is a systematic assessment undertaken that includes all aspects of loss of containment, including the frequency of occurrence and the severity of the consequences of such an incident, the possibility of ignition from the nearby unit/equipment leading to explosion and/or fire and the potential for escalation, to achieve an acceptable degree of fire safety of the plant.
What is FES?
Fire and Explosion Strategy is to verify and evaluate the potential fire and explosion scenarios on-site based on the findings from Fire and Explosion Risk Analysis (FERA) study conducted and specify the required fire and explosion protection strategy for the vulnerable assets e.g. critical equipment and buildings that could be impaired in potential fire and explosion.
What is FSAR?
Fire Safety Adequacy Review is to evaluate facilities fire and explosion risk, assess adequacy and effectiveness of the existing prevention, control and mitigation strategies.
Why do these assessment?
Smoke and Gas Impairment Analysis (SGIA) study is to assess the ability of the critical areas on the facilities to remain safe and habitable for the required endurance time during an emergency.
Methodology
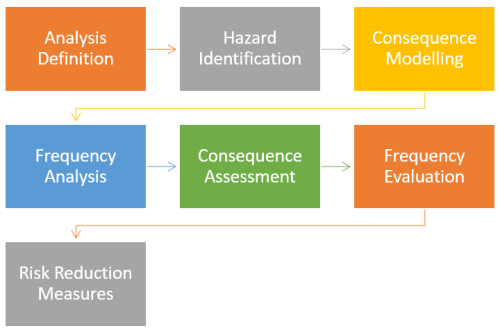
HSE & Fire Protection Design Philosophies
What is HSE & Fire Protection Design Philosophies?
HSE & Fire Protection Design Philosophies Philosophy are the basis for overall design philosophy for the Health, Safety and Environment as well as Fire Fighting Systems of a project to ensure a safe, risk-based approach to design is achieved, thus minimizing the possibility of injury to personnel, asset, environment and public from the consequences of an accidental event. This HSE Design Philosophy is a living document that has to be updated during the course of the project as necessary.
Why do HSE & Fire Protection Design Philosophies?
At the conceptual stage of any project, project teams must define a distinct HSE Philosophy that outlines the key business concepts to be embraced. The design contractors go over the Project HSE Philosophy in further depth, implementing their strategy based on the general and corporate philosophies.
The philosophy will apply to all design phases and as such will help ensure the design process:
- Results in a safe, reliable and operable facility through simple and effective design
- Minimises the overall loss of life and property damage at the facility.
- Minimises environmental impacts from planned and accidental discharges.
- Minimises unauthorized access to plant area.
It is a basic project requirement that appropriate safety features are incorporated during all phases of the design of the facility with a development life-cycle focus. The plant shall also comply with the Local Government Regulations and Legislations where applicable.