Safety & Risk
Our Safety and Risk Services
Formal Safety Assessment
HSE Design And Safety Case (Design And Operation Safety HSE Case), Quantitative Risk Assessment (QRA), Fire And Explosion Hazard Assessment (FERA), Escape, Evacuation And Rescue Assessment (EERA), Emergency Survivability System Assessment (ESSA), Temporary Refuge Impairment Analysis (TRIA), Smoke And Gas Ingress Analysis (SGIA), Dropped Object Study (DOS), Safety Critical Elements & Performance Standards (SCE PS)
Loss Prevention Studies
Firewater Demand And Hydraulic Analysis, Hazardous Area Classification (HAC), Safety Layouts And Drawings, Safety Equipment Datasheet And Specification, Fire Safety Assessment, Fire And Explosion Strategy (FES) & Fire Safety Adequacy Review (FSAR), HSE & Fire Protection Design Philosophies
Safety Workshops
Hazard And Operability (HAZOP), Hazard Identification (HAZID), Safety Integrity Level (SIL/IPF) Classification And Verification, Electrical Safety And Operability (ELSOR/SAFOP/EHAZOP), Health Risk Assessment (HRA), Constructability Review (CR)
Process and Fire Safety Audits
What is Fire and Process Safety Audits?
Process safety auditing is a set of engineering and management procedures for ensuring the safety of potentially hazardous processes. These systems’ flaws can put a facility at unnecessary risk. A process safety audit is conducted by a group of subject matter experts who identify gaps, compare the performance of these systems to best practises, and provide recommendations for how to close them.
Why do HSE & Fire Protection Design Philosophies?
The goal of fire and process safety auditing is to conduct a thorough, critical examination of all potential fire dangers in a building by detecting potential fire, explosion, and risk hazards and risks, as well as recommending appropriate preventive actions. They also ensure that the businesses properly comply with all legal standards.
The main benefits of fire safety audits are as follows:
- The safety procedures will be understood/aware by all employees.
- People who work in high-risk environments/conditions can be identified.
- Control measures that are already in place can be assessed.
- Determine if additional control measures are required.
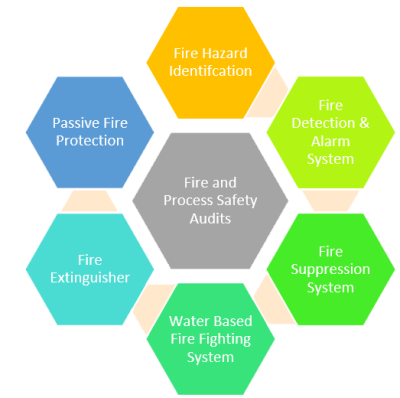
methodology
The following is the core methodology for fire safety auditing:
- The auditing team paid a visit to the site.
- The entire layout, blueprints, and layout of the premise are analysed.
- The firefighting apparatus in the facility is assessed.
- Employees’ training and awareness are assessed.
- Recommendations and necessary corrective measures are discussed.
- The team takes any necessary follow-up steps.
